Interview with Kara Harl, Managing Director of Dolcepack Sagl with AITI (Industrial Association in Ticino Switzerland)
A highly innovative company, Dolcepack Sagl was created and launched together with her husband Andrea Ferrari. Their professional partnership blossomed alongside their personal relationship.
Dolcepack, which ranked 4th in the Boldbrain Startup Challenge in November 2021, was founded in February 2020 by the husband-and-wife team Kara Harl and Andrea Ferrari. In reality, the idea of starting a business together originated much earlier, in 2007, shortly after they met.
At that time, both were engaged in their respective professional activities: Kara, an American, was living and working in Chicago, USA, while Andrea was living in Italy but already working for a Swiss company.
“We thought about starting our own business from the early days of our relationship, even though the idea was not yet well defined. When we saw each other, we would talk about it and think about how we could develop it,” Kara recalls with a touch of nostalgia for that intense and promising period. “Then, little by little, year after year, despite a thousand obstacles and difficulties of all kinds, we finally managed to make our dream come true, and now… here we are!”
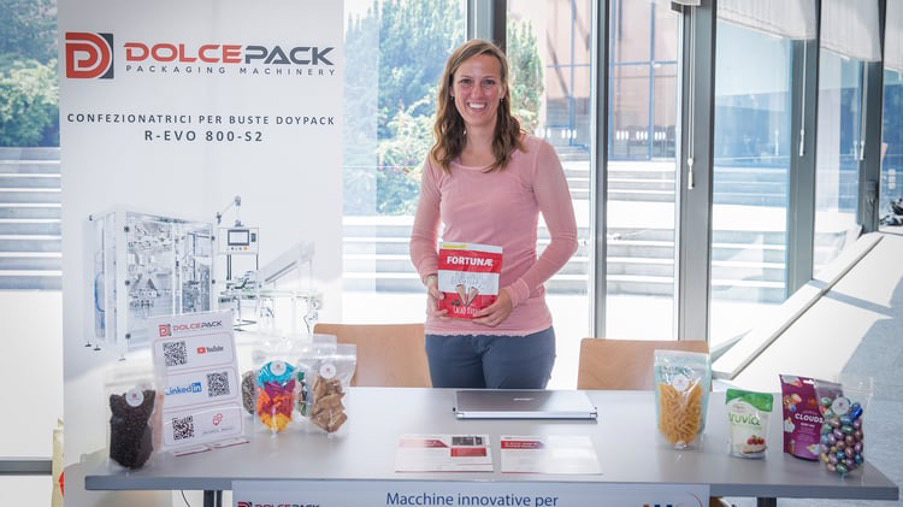
How did you and your husband Andrea meet?
In 2007, I was living in Chicago, working as a chemical engineer for a multinational company that created plastic products, specifically flexible packaging bags. Andrea, on the other hand, worked for a Swiss company that produced machinery for converting plastic into flexible bags, very similar to those made by my company. Working in the same field, it was perhaps inevitable that we would eventually cross paths. And indeed, that year, we met in California. My company was looking for machinery suitable for its type of production, and, as luck would have it, Andrea’s company produced exactly that kind of machine. The spark was immediate! We got married in 2008, and shortly after, I moved to Europe: for love, but also to pursue the business project we had developed in the meantime.
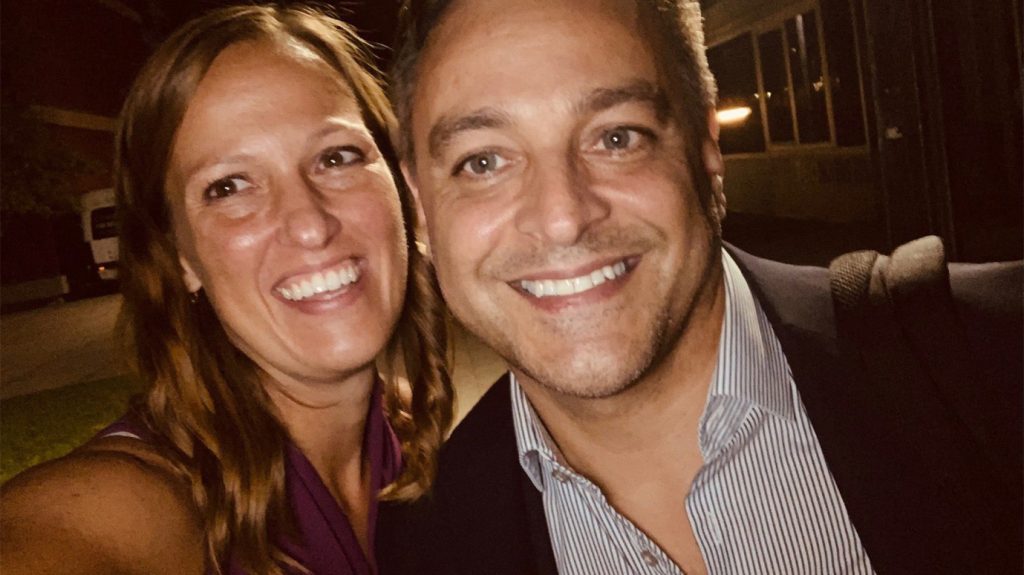
The core business of your company is quite clear: it’s condensed in the name “Dolcepack”…
Yes, indeed, the products filled and sealed by our machines are in many cases in the food sectors (solid and powder products). However, these preamde pouches can also be used in other industries: pharmaceuticals, cosmetics, detergents, and cleaning products.
Dolcepack, the name, expresses the kindness (“dolce”) that Andrea and I strive to put into all phases of our relationships with our customers. Providing reliable support and constantly engaging with those who have placed their trust in us and our machinery is truly essential for us.
Each of you, I understand, has brought your own skills and previous experiences to Dolcepack?
Exactly! I brought the wealth of knowledge and skills I gained in the plastic packaging chemical field: I studied the market, understood if there was potential for our products, and subsequently followed the procedural path that led to their patenting. Andrea, on the other hand, is the son of a mechanical designer-entrepreneur and grew up surrounded by drawings and machinery. Thus, he naturally acquired extensive knowledge of industrial automation (from weighing, to packaging, to product conversion), which is the foundation of Dolcepack machines.
What differentiates REVO – your flagship machine for filling and sealing preformed bags – from the more conventional ones available on the market?
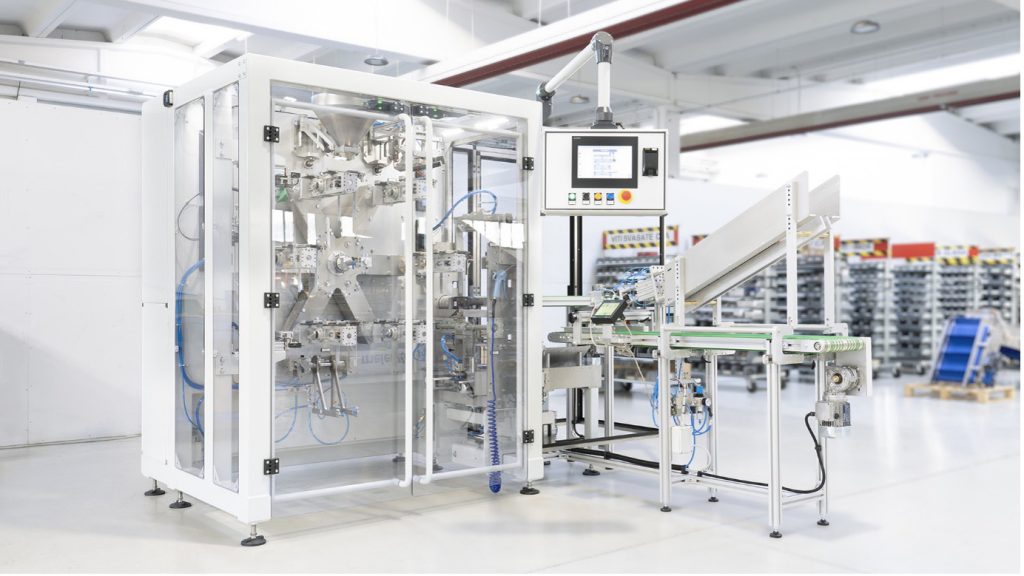
REVO was developed based on the limitations and shortcomings we observed in existing machines. Compared to conventional machinery, we rotated the so-called operational carousel by 90 degrees, allowing the operator standing in front of the machine to simultaneously see all the production steps.
In summary, what advantages does the implementation of REVO offer to companies?
The strength and innovative content of REVO lie in the comprehensive overview it provides! This results in significant and unprecedented advantages: the compactness of the machine (footprint reduced by approximately 60%), the packaging format change (which can be set automatically in less than 5 minutes without having to disassemble and reassemble parts of the machine), the reduction in the number of operators needed to operate and control the machine (from 2/3 to just 1), and reduced maintenance times. In short, the benefits of using our machine are truly numerous!
Who is responsible for the development and patenting of this innovative technology?
Well, I would say the development of REVO is entirely attributed to my husband Andrea, as well as its patenting. I, on the other hand, focused on thoroughly studying the competition and analyzing existing patents. Ours has always been a tandem effort!
What are your expectations for the near future?
Andrea and I, with the support of sales agents, are working to expand the sales network of our machines internationally. So far, we have focused on the European market and we are receiving good feedback from Switzerland, Italy, Germany, France, and Greece. Our machines can be considered 90% standard in their components. The remaining 10% needs to be customized based on the individual project and the type of product to be produced. This obviously facilitates production and, last but not least, optimizes costs.